I will never forget the excitement I felt the morning I first saw seafood sourcing data coming through US customs. It felt like a huge leap forward—but those feelings quickly faded when in audit after audit I realized how unreliable this information truly was. Nearly a decade of investment in supply chain digitization later and SIMP compliance is at an all-time low, with an audit failure rate now exceeding 50%.
Seafood trade faces a complex future of targeted import bans, digitizing EU catch certificates and a possible expansion of SIMP to all seafood on the horizon. Plus, industry is juggling these government requirements alongside increasingly complex demands from customers including vessel screening, reporting granular fishery details, and managing a wide array of certification, ranking and recommendation programs.
This isn’t just a red flag; it’s a breaking point.
After years of observing these trends, one thing became clear: supply chain integrity underpins all of these challenges. In this post I'll explain how Goldfish tackled the foundational 'garbage in, garbage out' problem in seafood traceability to make a solution that truly works.
Fixing the 'garbage in' problem
The first step was addressing the root issue: bad data inputs.
Sourcing information is often confusing, incomplete, and poorly controlled as it moves through supply chains. Spreadsheets can make the problem worse by separating data from important context in records, leading to confusion and errors.
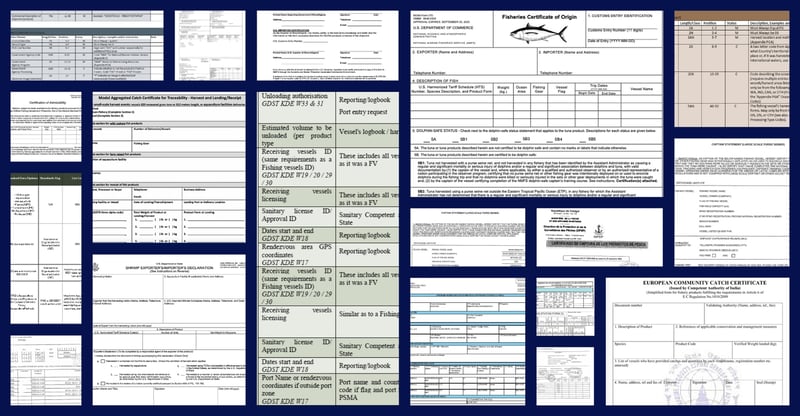
Standard traceability does a great job of making bad data look decent by organizing it into a clean interface, but here's the problem: a traceable lie is still a lie. It's still garbage.
Why doesn't traceability software keep the bad data out? It took me a long time to realize the simple answer: because these platforms weren't built by experts in seafood reporting requirements, so they have to accept everything as true. Most traceability software is repurposed from other industries and marketed as a fit for seafood. It’s the classic square peg in a round hole problem, and it isn't the only instance of the seafood sector being sold hand-me-down tech as a supply chain 'solution'. Another prime example is the widespread promotion of AIS (Automatic Identification System) data as a supply chain integrity tool. Vessel location information is shared to support safety at sea, not supply chain transparency. While it can provide insight into on-the-water activities in very limited circumstances, it’s ill-suited for validating vessel compliance or legality. Similarly, traceability platforms usually focus on generic supply chain risks without addressing the specific needs of seafood—which in reality are less about immutable data and more about incorrect data.
Clearly this approach isn't working.
Instead of trying to adapt another existing tool to seafood, we decided to start from scratch. What, in an ideal world, would a traceability system be able to do? We met with hundreds of industry experts to understand their pain points, and then we got to work.
First, we analyzed regulatory text, technical data reporting requirements for customs, official forms and more, then built a harmonized data input system tailored to those specific outputs. It required an extraordinary amount of time and level of subject matter expertise to understand how data requirements are articulated in both technical documents and in real-world practices. Without this groundwork we couldn’t have built a system designed specifically for seafood. We even found a few errors, and owe a h/t to FAO for adding the ASFIS species codes we requested!
Checking data
Once the 'garbage in' problem was addressed, we moved to the next challenge: ensuring the data was true. This meant asking tough questions, like:
- Does this species come from this area, and is it really caught using this type of gear?
- Is this a real fishing vessel, and is it operating legally?
Once again, we worked backwards from regulatory requirements to ensure that the validation datasets we standardize are actionable. For example—if you really think about it—what is needed to validate legal fishing isn't AIS data at all, it is linking sourcing information to managed fisheries and their associated vessels. Easy in theory, hard in practice.
Building standardized global datasets of fisheries, gear types, vessels, and more was incredibly hard, but at the time I thought we were just saving money until we could afford to buy this data from someone else. I didn’t expect us to be the first people in the world to create these datasets at this scale—but here we are.
For many of us who had grown accustomed to endlessly scrolling through convoluted websites this kind of screening tool looks like magic...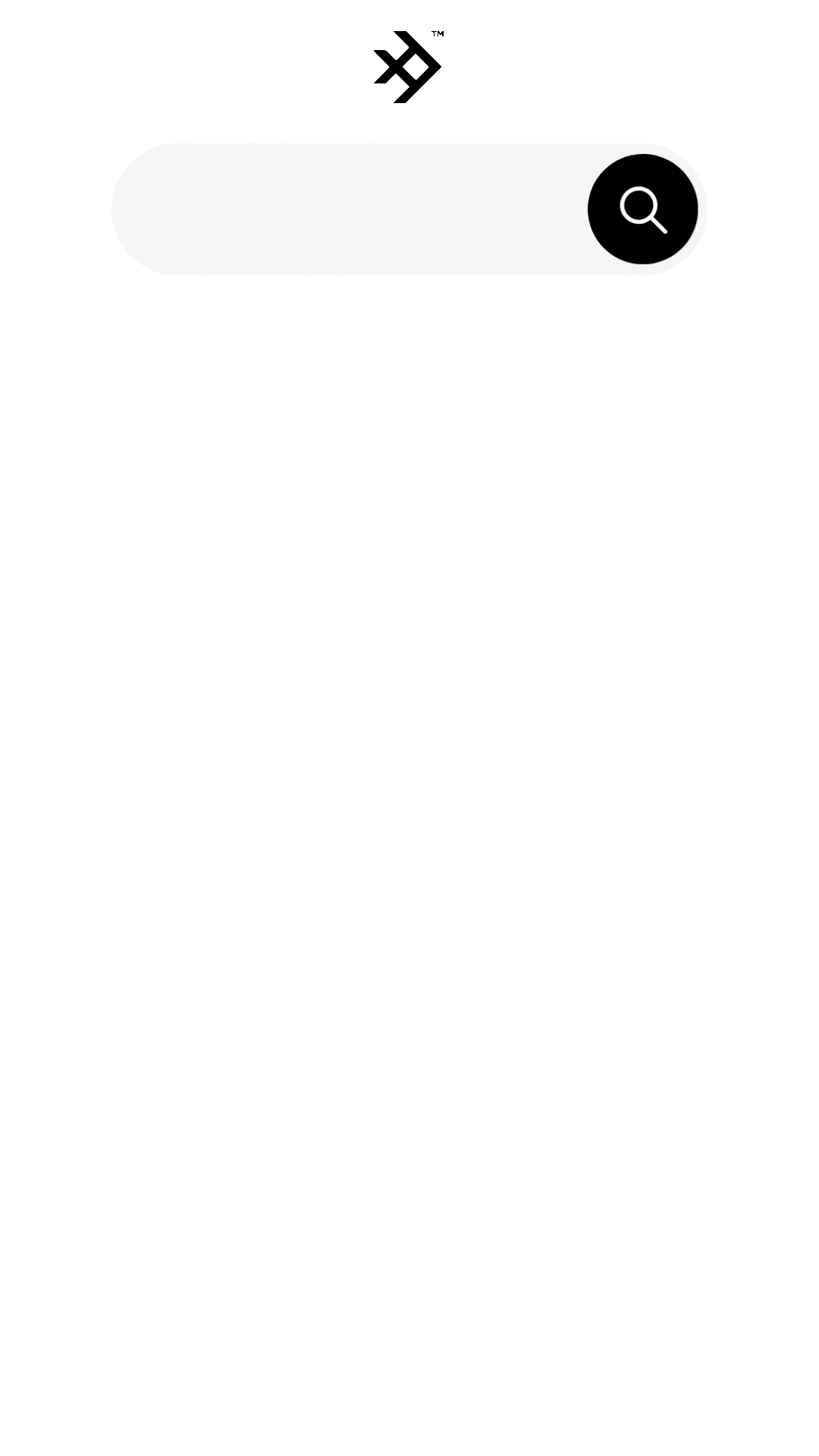
but it isn't! And it's free!
Structuring data
Next, we tackled the challenge of storing and structuring the data for interoperability. To us, interoperability isn’t a pay-to-play buzzword—it’s about making sure data moves seamlessly:
- from paper to digital and back again;
- from PDFs to spreadsheets to secure databases; and
- from tiny apps to giant ERP systems.
We use GS1 as the universal framework for structuring data because it is the most comprehensive and widely-used industry standard for supply chain management worldwide. In the few instances where GS1 lacks formatting instructions, we incorporate with GDST's standards to ensure that the data works across systems.
Storing data is just as important as structuring when it comes to interoperability, so we allow users to upload physical records associated with digital forms and meticulously log every change. This level of documentation supports audits and builds trust while allowing users to correct errors and make amendments if new information becomes available.
Making results tangible
Finally, we had to make the traceability actionable in real time—not just for the user entering data, but for multiple stakeholders. That’s where dashboards come in.
.jpg?width=800&height=450&name=Untitled%20(Website).jpg)
Our dashboards can be tailored to any user’s needs, offering a powerful way to visualize traceability data and risk in real time. This is a variation of one we built to help an organization track and mitigate risk in their vessel lists.
From form to function
All of this work culminates in our new Goldfish platform, which you can use to:
- Collect, validate, store, and share seafood traceability data
- Simplify FSMA-compliance.
- Collaborate seamlessly and securely with one-up, one-back supply chain partners.
- Customize forms to meet any and all regulatory and buyer requirements, and send them to partners to fill out for you.
We didn't enter the traceability landscape lightly-we set out to make a supply chain solution that truly works, and it led to a traceability solution organically. We’ve tackled the garbage in, garbage out problem in a completely new way—and we’re just getting started.
Ready to explore how Goldfish can transform your supply chain? Book a discovery call.
Want Goldfish screening in your platform? Explore our service provider partnerships.